Screw connections on critical infrastructures are exposed to major stresses and must therefore be checked on a regular basis. Researchers at the Fraunhofer Cluster of Excellence Cognitive Internet Technologies CCIT have now developed a technology that allows the stability of the screw connections to be checked at any time by remote monitoring. This increases safety and reduces the time and effort spent on inspections.
We come across screws almost everywhere. For instance, on cranes, scaffolding, high-rise buildings, bridges, wind turbines and machines of all sizes as well as in production facilities. However, wear and tear and the impact from phenomena such as temperature fluctuations or vibrations can cause one or more screws to loosen or even come undone completely. This can have fatal repercussions. As a result, regular inspections are required for safety-critical structures. A team of researchers from the Fraunhofer Cluster of Excellence Cognitive Internet Technologies CCIT has now developed a solution called “Smart Screw Connection” that combines sensors and radio technology to provide a reliable means of remotely monitoring the screw connections – not to mention that it is self-powered.
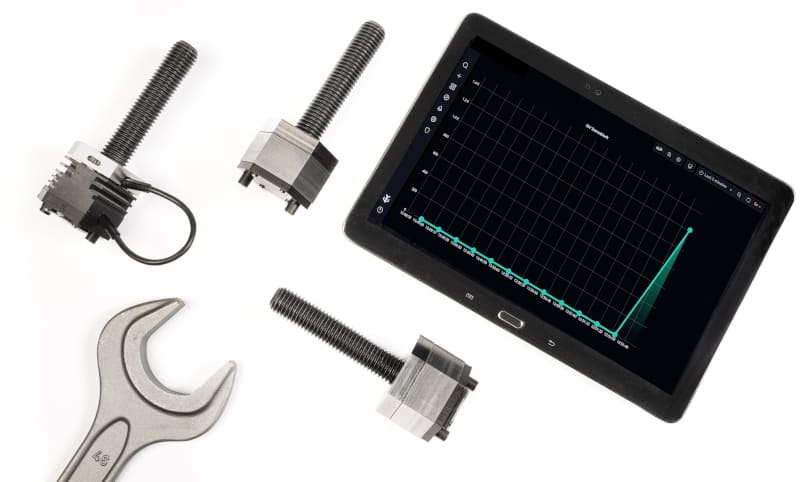
The Smart Screw Connection comes with a screw fitted with a washer that is equipped with a piezoresistive DiaForce® thin film. When the screw is tightened, the pressure-sensitive sensors register the preload force at three points. Any change in the preload force changes the electrical resistance in the DiaForce® thin film. “When a screw comes loose, the resulting change in resistance is reported to a radio module located on the screw head. The radio module, in turn, sends the data to a base station, which collects the information from all relevant screws in the object,” explains Dr. Peter Spies, Project Manager and Group Manager Integrated Energy Supplies at the Fraunhofer Institute for Integrated Circuits IIS.
Reliable data transmission via the mioty® protocol
The DiaForce® thin film was developed by the Fraunhofer Institute for Surface Engineering and Thin Films IST. In terms of radio technology, Fraunhofer IIS has contributed the mioty® low-power wide-area network (LPWAN) protocol. This technology is capable of sending small packets of data over long distances, consuming minimal energy, from more than 100,000 sensors via just one base station. The base station could be located at the edge of a wind farm, i.e., several hundred meters or even a few kilometers away. A software program then displays the data for each individual screw in a graphical overview. Depending on the configuration and application, the status of the screw connections is transmitted permanently, based on an event or at specified intervals.
“This remote monitoring system allows us, for the first time, to keep an eye on the stability of safety-critical infrastructures at all times, even remotely, and to carry out a proper check on every single relevant screw. This is a major asset in terms of safety. When inspecting a bridge or wind turbine, no engineer is required to be on site and check each screw individually, as all the data are transmitted via radio to the service station,” says Spies.
The Smart Screw Connection can be adapted for a wide variety of applications. No matter whether it’s for flange connections in industry, for the bolts in steel girders in high-rise buildings, for the load-bearing parts of bridges or for attaching rotors to wind turbines – the system can be individually configured for each scenario and adapted to the relevant load profile.
The researchers have also resolved the problem of energy demand in a resource-efficient manner. The system operates according to the energy harvesting principle. This involves the use of heat or light to generate electricity. In this system, for example, a thermoelectric generator generates electricity from the minute differences in temperature between the screw head and the environment. It is also possible to generate the electricity through solar cells. Energy harvesting makes the system self-powered.
Encryption protects against hacker attacks
Security is of paramount importance to the Fraunhofer researchers. During installation, each individual screw, along with the sensor unit and radio module, is placed in a shielded programming box. The box is giving the screw an individual ID via the short-range RFID, as well as its requirement profile and an individual encryption key. The radio link from the screws to the base station is also encrypted during data transmission. “This is how we prevent criminals or hackers from sabotaging the system. The technical staff who monitor a wind turbine, for example, can really rely on the data,” explains Spies.
Fraunhofer IST, Fraunhofer IIS, as well as the Fraunhofer Institute for Structural Durability and System Reliability LBF and the Fraunhofer Institute for Applied and Integrated Security AISEC are involved in the project being run by the Fraunhofer Cluster of Excellence Cognitive Internet Technologies CCIT.
The technology is designed for commercially available DIN screws. The system is ready to use for M18 screws, and versions will soon be available for M20 and M36 screws. A demonstration version will be exhibited at the Hannover Messe 2022 (May 30–June 2) (Hall 5, Booth A06).
On Tuesday, May 31 from 4:30 p.m. to 5:30 p.m., interested visitors can also learn more about the technology and availability of this development in the presentation and networking space of the joint Fraunhofer booth in Hall 5-A06.