In the U.S., demand for workers in the food processing industry remains high. Nut sorting is labour intensive, but a processing plant is showing how robotics is freeing up the manual workforce requirement while improving process quality. 100 SCARA robots on a nut sorting line are increasing efficiency and reducing the total cost of ownership, as well as adding process accuracy. Along with vision system integration, a single motion controller manages each SCARA robot pair, minimising the total budget outlay.
Hosting 50 pairs of Trio SCARA robots, a new nut sorting conveyor at a large processing facility in the U.S. is handling a much greater throughput than a traditional manual line. Operating 24/7, the robot system has presented double digit percentage growth in productivity and is freeing up the need for tens of workers across several rotating shift patterns.
With an employment rate of around 96.3% in the U.S.[1], the effects of the Great Resignation are still being felt across various American industries, including food processing. In this sector, the demand for workers is high, with an average annual workforce growth reported as high as 27%[2] between 2014 and 2021. Instead of having to rely on manual sorting, and the challenges that brings in workforce recruitment and retention, integrating robotics is helping the nut processing facility increase production.
A rise in robotics is also extending the potential to improve working conditions. At the plant, baked or shelled nuts are fed onto a conveyor, where operatives positioned along the line look for, and then remove, sub-quality produce. The conveyor is constantly moving for relatively long periods, while workers have to focus their eyes and repeatedly pick defective nuts. The new SCARA conveyor is in addition to the existing manual lines and has increased capacity at the facility. But, in future, replacing the manual lines with SCARA automation can enable workforce redeployment into less physically taxing, and more cognitively involved tasks.
SCARA increases productivity
Automating nut processing at the facility is not only increasing throughput, but is also improving product quality and consistency too, compared to traditional sorting. With the manual approach, defining a defective item can be subjective from person to person, and so can the ability to spot an unwanted nut, so consistency can vary. To ensure productivity, the conveyor is relatively fast moving, so the manual process also has to be completed at speed, balancing throughput with accuracy.
But substituting humans for robots on the nut sorting line requires seamless integration within the automated system, combined with high robotic motion coordination. First, the robot has to spot a defective nut, then it has to be able to quickly pick it with the necessary dexterity to grip and hold very small, non-uniform items.
On the new conveyor line, each SCARA robot pair connects to a camera vision system that plots precise coordinates to sub-millimetre accuracy. The vision system identifies defective nuts, and the SCARA pair then guides their gripper to pick and remove the unwanted produce.
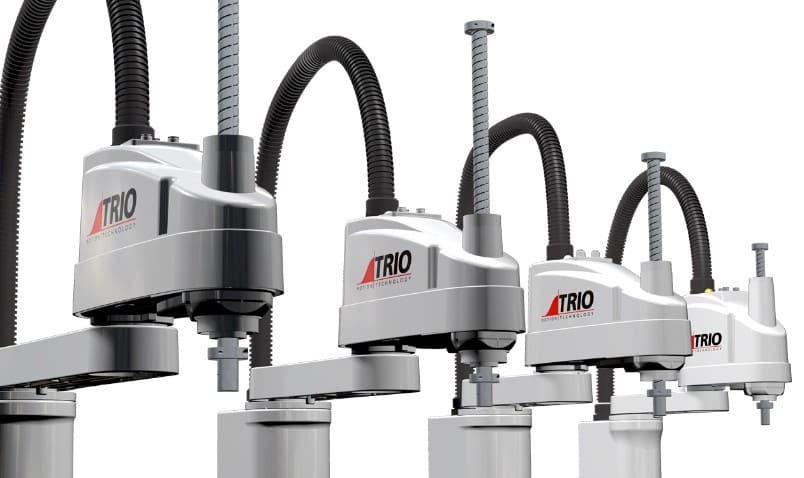
A SCARA robot, the acronym for Selective Compliance Assembly Robot Arm, is ideal for this process thanks to its compact footprint, enabling the integration of multiple ‘pickers’ along the conveyor line. Rigid in their vertical axis but with freedom on the horizontal plane, SCARAs are designed for operation over a controlled path and can optimise productivity thanks to their speed and precision. Crucial to the intricacy of picking a small nut at speed is the robot’s end effector, which features a three-pronged gripper.
Speed and precision in SCARA control
Responsible for coordinating both SCARA pair, as well as the camera vision system, is a single Trio Flex-X Nano motion controller. The Trio Flex-X Nano also controls the motion of the grippers. XYZ-Theta axis control of the grippers gives three-dimensional motion, plus rotation, and also controls their opening/closing movement.
The Trio controller features deterministic, real-time EtherCAT communications down to 125µsec, with an execution benchmark of 125 lines/ms. This gives high speed commands to the robots, while Trio’s SCARAs achieve repeatability down to ±0.1mm and ±0.01°. This combination of speed and precision ensures high speed identification and picking, while optimising quality through consistency.
The 50 robot pairs cover a conveyor system around 50m long. This extended length and high concentration of robots ensures a refined level of sorting, giving the highest quality end produce. A single controller for each robot pair, instead of a typical approach of one controller for each robot, has also reduced the total cost in hardware, including cabling.
IoT integration
While the controllers coordinate the motion of each tandem of SCARAs, they also need to coordinate with the motion of the conveyor. Integration with the plant’s existing control architecture means that the Trio controllers connect to the hierarchy via Modbus. The automated line is also enabling IoT efficiency gains through real-time data management, combined with remote monitoring.
Trio developed the motion profiles and automation programming in IEC languages, and the company’s U.S. team is supporting the plant’s automation engineers. Though the new conveyor has only recently gone live, as a result of the increased productivity and quality gains that are already evident, the plant is now planning the introduction of further automated SCARA processing lines.