One of the most important manufacturers of frozen hamburgers in the US, White Castle, is using ABB robots to optimize its production and avoid injuries to its employees. White Castle sells its popular range of frozen mini burgers, or ‘sliders’, to stores across the United States.
At its Louisville, Kentucky, frozen food plant, precooked hamburger meat arrives in the form of logs and is cut into individual patties. The patties are manually placed on the bottom of the bun and then topped with grilled onions and cheese and the top bun. Full sliders are flow wrapped two-in-a-pack and transferred to a blast freezer.
From here, the packages are placed on a conveyor that leads to three separate packing lines: two parallel lines for 12-count boxes sold at general retail stores and a separate line for 16-count boxes sold at wholesale clubs.
As production of sliders increased, the company noticed several process bottlenecks, most notably packing two-pack sliders into retail cartons, a highly repetitive task that involved handling frozen products.
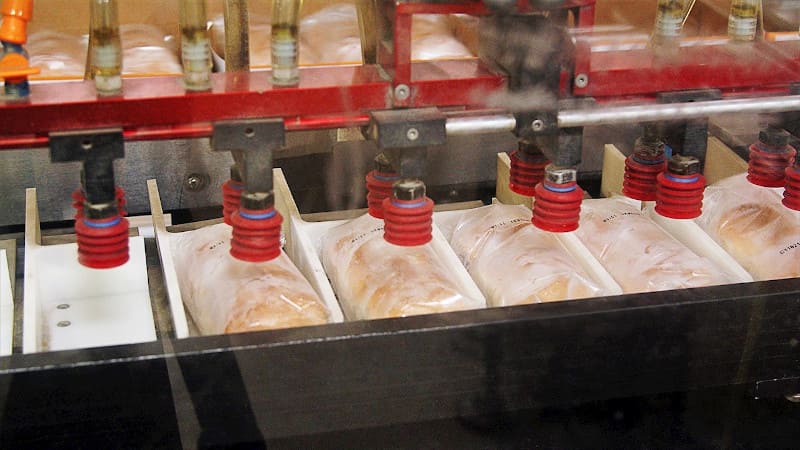
To speed up this process and move employees to less physically stressful jobs, in 1998 the company installed an IRB 340 FlexPicker® on each of the lines. Equipped with vacuum grippers and sophisticated motion control, each IRB 340 robot in the 12-unit carton lines picks six packs from two sliders at a time, while a newer IRB 360 FlexPicker in the 16-unit line picks eight packs. two at a time. time.
In each cycle, the robots pack a layer of two cartons simultaneously, with two pick and place iterations completing two cartons at a time. Each of the original IRB 340 models is still in operation at the Louisville plant, more than twenty years later.
Optimizing designs with ABB RobotStudio
White Castle also later installed additional robotic cells on two other areas of the parallel lines – one to pack the retail cartons into 12-count shipper cases, and one to palletize the shipper cases onto 96-case pallets. These original robots served their purpose for many years, but eventually approached obsolescence.
White Castle called in CIM SYSTEMS INC., an authorized ABB robotic systems integrator, to find replacement solutions for the carton packing and palletizing area.
“The ABB delta robots are the best investment we ever made, Their speed and accuracy keep the lines moving and they are highly reliable. We have taken great care to maintain them, and we will continue to do so. I think they will last a good while longer.”
Plant Manager Tony McGraw.
The new palletizing system presented some design challenges. The first was a tight palletizing area which needed to fit two full lines. The solution was to position the end of the conveyor from each line perpendicular to the front of the robot, one just beyond the other, with a pallet station along the right side of the robot.
White Castle also wanted the robot to pick empty 45-pound pallets off a stack and place them in the build station once a previous pallet had been built and moved to the stretch wrap station. This required a more complex end effector design and intricate robot motion.
To develop the solution design, CIM used RobotStudio®, ABB’s offline programming software, to simulate the palletizing cell, including the specialized end effector, and determine the optimal robot position and motion. Using the software also helped to identify any bottlenecks as well as calculate accurate space requirements and cycle time.
CIM needed to coordinate the robot motion and pallet pattern, making sure the load would clear the first pallet, no matter its height, to safely reach the second pallet.
The end effector was bigger than most because of the need to pick up both cases and pallets. It features vacuum cups that pick three eight-pound cases at a time for the palletizing operation, along with four pneumatically operated hooks positioned on each corner to securely handle each empty pallet. This combination enables the robot to execute both functions without requiring a tool change.
RobotStudio helped CIM design and prove the performance of the system while accommodating all the variables. The palletizing robot used in this system is an ABB, 4-axis IRB 660 with a 3.15 meter reach and a 180 kilogram payload. This configuration provides enough length and strength to reach and clear all points in the palletizing cell from a stationary position, both horizontally and vertically.
New robots for case packing station
White Castle’s latest automation installation features two-ABB IRB 1200 robots that pack the retail cartons into twelve-count shipper cases – this station is sited after the packaging line and before the palletizing robots. Mounted on a common pedestal between the two packaging lines, the two lower-payload robots use vacuum end effectors to pick two retail cartons at a time and place them into the cases.
The new 5 kg case-packing ABB robots, one dedicated to each line, replace a single, larger robot that served both lines with dwindling efficiency as production volumes increased. Manual operators, who were previously required to assist the process, have been moved to more rewarding jobs in the facility.
CIM again used RobotStudio to identify the optimal positioning of the robots based on their footprint, reach and payload, and to validate the requisite system performance in relation to the existing components of the packaging line.