As part of Industry 4.0, the value chain of manufacturing companies is being more and more digitised. On the one hand, digitisation helps to capture detailed information on resources, associated processes and manufactured products. On the other hand, using this information permits extensive production and product improvements and contributes significantly towards enhanced efficiency and effectivity. In this context, the digital twin of an object in production is a digital representation of a specific product (real-world object, service or immaterial asset) which uses models, information and data to reflect that product’s properties, state and performance . It is able to adopt the data of its real-world counterpart as a digital shadow, upgrade this data to information through semantic connection and finally integrate it into simulation and other product models.
Linking the digital twins of different production components with each other forms the foundation of a consistent information base along the value chain. The digital twins’ interoperability guarantees the vertical and horizontal integration of all components across hierarchical levels and disciplinary boundaries. In addition to information with clear unambiguous semantics, this also requires the definition of joint interfaces supporting the exchange of information.
Digital twins in the process industry
Value creation in a chemical plant consists in manufacturing products from educts. This is why the main business process follows the supply chain. However, assets are needed to enable production to take place in the first place. Assets have a life cycle of their own, consisting of various phases such as process development, engineering, manufacture, assembly and commissioning, operation and dismantling. The operating phase also comprises concurrent maintenance, testing and optimisation processes. All these processes require information from different disciplines and companies which they process and from which they generate new information.
The sensors installed in the assets also produce a host of information. This information is condensed along the automation pyramid and used for process control as well as maintenance, analysis, optimisation, etc. Process data is increasingly also being used in digital business models, e.g., when asset suppliers use sensor readings to generate after-sales services.
Nowadays, contractors mostly submit a number of documents as a result of their work. These may be planning documents such as datasheets and flow charts, but also test or maintenance reports. The documents are usually submitted as hard copies and pdf files. Some documents, e.g., flow charts, are provided as editable graphic formats. Often 3D models are not editable or have lost any relation to the P&I diagram, if there had ever been one at all. In future, data will be handed over in addition to documents. The members of NAMUR Working Group 1.3 feel that this transition from document handover to data handover is a major factor in digitising the process industry , even though documents (e.g., according to VDI 2770) will continue to exist in their own right for formal or legal reasons.
In the light of the phases of the asset life cycle, NAMUR WG 1.3 found the structural setup shown in Figure 1 useful for a realistic representation of the information volume of a process plant. The plant model contains the structure model of the plant. It is mostly developed during the engineering phase (original draft) and provides the information necessary which may be represented graphically as P&I diagrams or form the basis for specification sheets. It also stores information on the process to be run on the plant. This information is represented in classic process flow diagrams.
The basis of this structure model consists of simulations performed during process development. The simulation models needed for this purpose map behaviour and performance which is a characteristic feature of a digital twin. The models describe material properties, store the equations and kinetics of the chemical reactions taking place and, where appropriate, use empirical models as a basis for artificial intelligence. During process development, these simulation models are used to identify the ‘best’ plant structure for the chemical process in hand through iteration and to design the package units and incorporate them more easily into the overall plant. Once redlinings from assembly and commissioning have been integrated into the structure model, both the plant model and the simulation model can be accessed in the operating phase. Simulation models may be used with different levels of detail for optimisation, advanced process control, operator training or asset performance (in part adopted from .
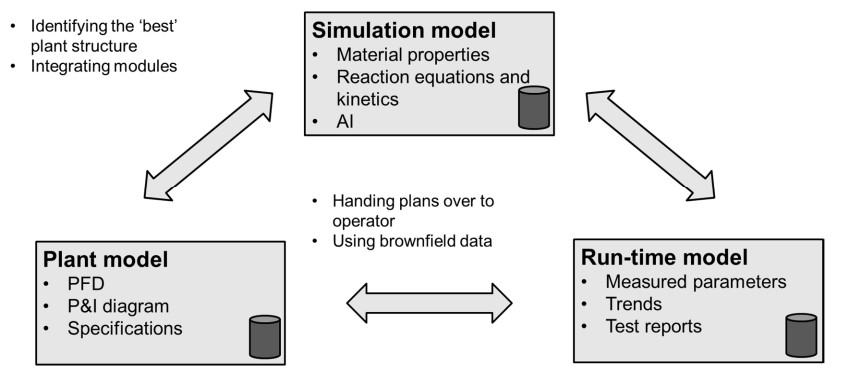
Figure 1: Information models in the digital twin
Hence, the digital twin may be regarded as a compilation of different simulation and information models describing the structure, function and performance as well as built-in equipment and necessary maintenance activities of a process plant. Information models give the different types of data syntax and semantics and aggregate them in a digital twin. Functions processing information can access the various sources in a digital twin via interfaces. Given the large number of customised software, especially in the operating phase of a plant, the authors do not think that in future there will be the database or tool containing all the information needed.
However, information models permit the overarching interpretation of data based on a shared understanding. Another benefit is that it is easier to create interfaces between the systems. All that is necessary is to create in each tool a standardised import/export interface based on the information models of the digital twin via which information recipients with subscription mechanisms can retrieve information on necessary updates. Proprietary interfaces between individual tools are not necessary. The structure identifier supports interconnecting the various information aspects of the plant model. Connecting the role information of the structure identifier with the current instances of equipment installation provides a connection with their Asset Administration Shells. The digital type plate and asset identification according to IEC 61406 (formerly DIN SPEC 91406) permit the interconnection of the various information aspects. There is already a number of sub-models for the areas of structure models and runtime models shown in Figure 1 These sub-models are shown in Figure 2.

Figure 2: Sub-models of the digital twin
This figure covers a number of areas which will be explained below. The vertical bar separates the engineering and operation phases. However, there are overarching information models which form the basis for all following information models. First of all, these are dictionaries like IEC 61987 or ECLASS which provide definite identification keys by means of IRDI (International Registration Data Identifier) so that information models based on it can establish a semantic relationship. The Asset Administration Shell according to IEC 63278-1 Ed.1 provides the possibility to implement a digital twin which can be used both as data container and information broker (see [5]). In the operation phase, OPC UA provides a standardised communication tool.
Plant models can be broken down into structure models and asset models. As the name indicates, structure models provide information on the structure of the plant and the requirements to be met by the role, i.e.,
specification information. These models are mostly used for engineering purposes. Asset models describe the real assets in the plant, e.g., equipment, machines, measuring instruments, final control elements or motors. The assets have to meet the requirements defined by the role. The runtime models shown in Figure 2 are needed for modelling operation
Relationship with the Asset Administration Shell
The Asset Administration Shell consists of a number of information models describing all information about, and functions of, a certain asset, including its features, characteristics, properties, status, parameters, measurement data and capabilities. The Asset Administration Shell covers the entire life cycle of products, equipment, machines and plants. A digital twin is the virtual representation or model of a real-world object. Currently, the Asset Administration Shell is the most promising technical construct to implement digital twins. It contains a compilation of different information models, with each model looking at the object to be modelled from a different perspective.
Benefits of the digital twin
Using a digital twin offers a number of benefits which justify its introduction in spite of additional cost and effort. This additional effort results especially from the subsequent generation and implementation of the digital representation of an existing (brownfield) plant, but additional effort is also required for the early integration of a digital twin into engineering a newly planned (greenfield) plant. It has not been possible so far to perform and validate a general analysis of the cost-benefit balance so that using a digital twin will always have to be considered in relation to the project in hand.
Nevertheless, digital plant models improve the consistency of documentation over the plant life cycle. This offers a better starting position for optimisation, expansion or replanning. Integrating planning, live and historical data permits improved concept planning, design and commissioning in the engineering phase. Enhanced functions and services such as automatic operating and process optimisation or preventive maintenance provide support during the operating phase. [5]
It is only with defined standardised syntax and semantics (e.g., like for the Asset Administration Shell) that the digital twin can ensure data and information consistency and permit the shared use and updating of an
information source. Automated data transmission from one sub-model to another can substantially contribute to reducing the number of transmission errors that occur in currently common manual data transmission. Transfers between operators and contractors also offer a major savings potential. Contractors receive standardised submodels from operators and/or are granted access to a shared information source so that they can develop compliant and agreed asset models in the tools they are familiar with, work on them and then restore them to the digital twin.
The authors have identified an important benefit at the transition from planning to operation, in particular. There are two reasons why the commissioning phase is of special interest. On the one hand, the product to be manufactured has often already been sold in advance at a fixed date so that delayed commissioning would result in a financial loss. On the other hand, the accounting aspect is a challenge since this is the transition from CapEx to OpEx. In this phase the digital twin can provide different simulation solutions to help with evaluating design decisions, the qualitative development of a control solution, virtual pre-commissioning and earlier operator training. In this way, the engineering phase can be shortened and harmonised and a trouble-free start of production achieved. Operation of the plant, though, is another important phase for working with the digital twin. Since it can provide the necessary information on plant, operation and product in a targeted manner, the digital twin permits tapping additional savings potential and increasing efficiency and effectivity. In-process monitoring helps to identify and correct process deviations at an early stage to ensure consistent high product quality. By monitoring the status of process-critical components, predictive maintenance can reduce plant downtime, thus increasing overall productivity. However, these applications are just examples which can be varied in many ways and to which many others can be added. [1, 7, 8]