Automating any processes in a production sequence can simplify operational challenges as well as increasing efficiency and quality. Yamaha Motor Robotics FA Section has helped companies in different sectors of the food industry to realise these benefits by introducing robots to handle packaging and labelling.
One of Yamaha’s customers in food production, an established brand of baked sweets with a history stretching back over 100 years, recently installed an array of SCARA robots to optimise production capacity when packing the sweets into boxes of various sizes.
Using conventional manual packaging, a different number of workers is needed in the production area at any given time, depending on the numbers of boxes ordered and the quantity of sweets to be packed. Figure 1 illustrates workstations in the production area. The table shows how the optimum number of workers fluctuates according to the production target. This challenges managers to ensure that only the required number of workers is present on a daily basis.

“Our team analysed the workflow in the packaging area and proposed an array of eight YK400XE SCARA robots, linked using LCMR200 linear conveyor modules,” explains Jumpei Ninomiya, Sales Manager, Yamaha Motor Europe Robotics Business, Factory Automation Section. “Only one worker is needed to supervise the robots, which eases the management of human resources and stabilises production, ensuring that all orders can be fulfilled efficiently.”
With 400mm arm length and 4kg payload capacity, the YK400XE is the smallest in the high-performance, affordable YK-XE series. It is ideal for palletising, loading/unloading, assembly and inspection tasks and is easily connected to Yamaha’s RCX340 controller to unleash the full potential of its features. These include automatic optimisation of acceleration and deceleration, which enhances control – especially when moving a heavy load – while also optimising reliability and minimising vibration.
As a further enhancement in the sweet packaging application, integrating the RCXiVY2+ vision system enabled each YK400XE to check the orientation and position of each individual item to be packed. The modernised production area (figure 2) can now operate continuously for 24 hours per day, with supervisors working 8-hour shifts. The LCMR200 conveyor modules give the flexibility to adjust the conveyor stop position quickly to handle boxes of different sizes.

A spokesperson for the company added, “In addition to delivering the expected labour savings, our new Yamaha SCARA robots have improved productivity, reduced costs, and reduced human errors thereby enhancing quality. They are enabling us to preserve our history and tradition while modernising our processes and delivering even more delicious baked sweets to our customers.”
Companies handling foods such as meat products can face a rather different challenge. The environment where the meat is handled must be kept at a constant 4°C. Humans cannot work safely in such conditions for a long period.
Yamaha’s latest customer in the food business has successfully automated the labeling of fresh meat packages in cold conditions using YK-TW SCARA Robots. The company’s production managers had previously contemplated using a parallel link robot, which is a common sight in many factories. They discovered that these tend to be large and heavy machines that require a strongly engineered gantry with securing anchors. Feeling that this would be impractical to install in the factory, they approached Yamaha for a more suitable solution.
Their new Yamaha YK-TW orbit type SCARA robot is integrated with a machine vision to recognise the packages and detect the position for label adhesion (figure 3).
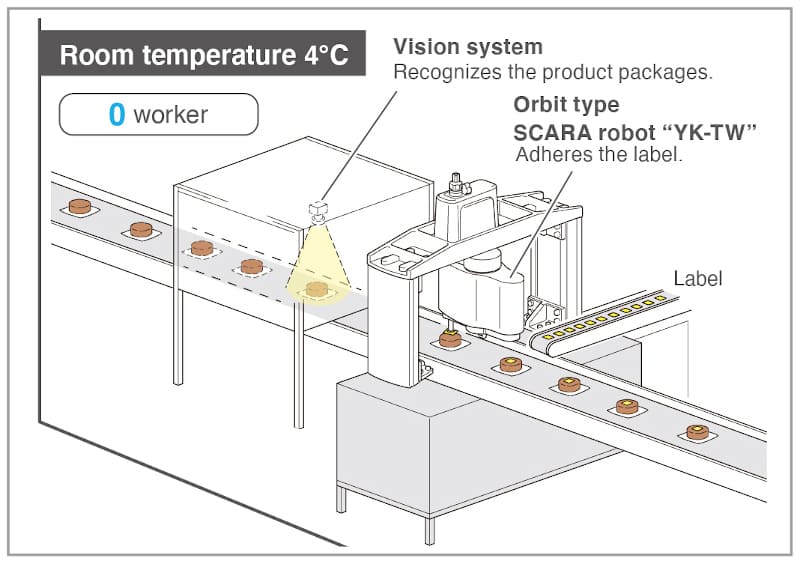
Specially designed for gantry mounting, the omnidirectional YK-TW eliminates the shortcomings of conventional parallel-link robots. Its relatively light weight and lower overall height equate to much lower inertia, so there is no need for a bulky frame. In addition, it comes with an optional purpose-designed genuine Yamaha mounting bracket that saves the engineering overheads associated with designing a custom gantry.
“This company had never used robots before, so our team helped them perform a preliminary evaluation with the YK-TW to confirm that it would meet their requirements,” explains Jumpei Ninomiya. “Many customers choose the YK-TW because it can work in narrow spaces. The R-axis can pass completely under the main unit to make full use of the workspace below and the moving parts are optimally balanced to enable efficient movement at high speed with consistent accuracy.”
A spokesperson for the company added, “Since installing our Yamaha robots, demand has increased for our chilled products and frozen foods, Thanks to the compactness of the YK-TW and its mounting, we are able to change the factory layout easily and add extra production lines to increase capacity.”
For food production, as well as semiconductor manufacturing, medical, and pharmaceutical applications Yamaha also has a selection of clean robots including YK-XGC/XC SCARA, FLIP-XC single-axis, and XY-XC cartesian types. Meeting internationally recognised cleanliness standards such as ISO 14644-1 class 3 and FED-STD-209D class 10, they employ features such as beltless design and air suction to ensure low particle emission.
“Our Yamaha SCARA robots enabled both of the customers in this study to achieve their main goal to minimise labour costs. In each case they were also able to improve quality and productivity, and simplify management of production and resources. They were also able to increase output quickly to take advantage of new market opportunities,” summarizes Jumpei Ninomiya.
He concludes “For companies in food, or indeed in many other production and packaging industries, that first small step into automation can begin a journey that delivers increasing returns through ongoing investment.”