An industrial robot can be as simple as a single-axis robot for basic transport and position, or can be scaled up to multiple axes working in concert. The latest single-axis models bring together advanced design features and software tools to enhance accuracy, speed, and ease of use
Industrial robots are known to boost productivity. Moreover, and since the pandemic, it is clear they can safeguard workers’ health by reducing staffing on the factory floor and reducing human contact with components and assemblies. Among the various types of robots that are available, single-axis robots are easy to understand and use. They are already automating a wide variety of tasks in factories and logistics hubs; sometimes operating in isolation, often configured in groups co-ordinated by a central controller. Always, they bring greater throughput, repeatability, and consistency to operations.
System integrators can develop systems based on single-axis robots in one, two, or three axes to tackle handling and assembly challenges. These can include transferring bulk items into individual trays or pallets, sequences such as feeding and cutting, and positioning jigs and tools.
On the other hand, two or more linear units can work together to perform tasks that demand high accuracy like laser cutting, painting, or dispensing. A custom cartesian robot can be built by combining single-axis robots specially selected for each axis (figure 1). Yamaha also has a range of standard cartesian robots, available off the shelf.
A linear unit can also act in concert with a cartesian robot, connected to the same controller, in situations that require more axes. A controller such as the Yamaha RCX340 is usually chosen to manage the cartesian robot. It has the capacity to control one or more additional single-axis robots working as part of the same unified, coordinated system. This lets integrators configure robots to handle complex sequences, with the flexibility to expand the system if needed.
What to Look For
Rigidity is one of the most important properties of a single-axis robot, needed to ensure precise and repeatable positioning and allow the slider to move freely with minimal friction. The design of associated mountings and supports can also be simplified, saving both space and cost. On the other hand, compact dimensions are also desired to minimise the factory area occupied by the robot. Using advanced design techniques, it is possible to achieve a reduction in size at the same time as increasing rigidity in every axis.
The latest high-rigidity single-axis robots in Yamaha’s Robonity series feature one-piece construction and a built-in linear guide. These enhancements have increased the rigidity by up to 300% while at the same time reducing the rail width. The ABAR05 (figure 2) is just 54mm wide, a saving of 17% compared to typical alternative models. No external guide is required, which simplifies design, and the increased rigidity preserves the robot’s straight-line performance when subjected to a radial load. The play in the direction of rotation is inhibited and tools attached to the tip of the rod achieve ±0° of non-rotating accuracy. The robots are available with stroke length up to 1100mm.
The latest design enhancements have also allowed the overall height to be reduced. A major advantage of these new, slimmer robots is that the centre of gravity is lowered, which enhances performance when used as the x-axis of a custom-built cartesian robot. The ABAS12 is 76mm high and 120mm wide. In addition, the latest design maximises the movement stroke in relation to the total length. Together, the reduced length, width, and height, with increased rigidity, and comparable range of movement compared to alternative models, all contribute to enabling a significant downsizing of facility equipment.
There are further space savings to be gained in the design of the control panel. The EP-01 controller for Robonity robots is 37% narrower than alternative modules, at 40mm wide.
Selecting the Right Model
When selecting a single-axis robot, the type of motor should also be considered. Yamaha’s Robonity series contains robots with a ground ball screw designed for use with a servo motor. The range contains complete units capable of speeds up to 2400mm/s. There are also motorless actuators that are compatible with industry-standard motors up to 400 Watts. Attachment kits are available that allow changing the motor orientation to suit the requirements of the application.
Alternatively, stepper motor robots such as the Transervo series can provide a cost-effective solution with the functionality of a servo motor for applications that require lower payload and ultimate speed is not a concern. The latest models can handle almost four times the payload of their predecessors, and the excursion speed of 1200mm/s is 20% faster.
On the other hand, a linear-motor single-axis robot could be the most cost-effective solution for an application that demands transporting lightweight workpieces over long distances at high speeds. Robots are available with maximum stroke greater than four metres and maximum speed of 2500mm/s, with ±5µm repeated position accuracy. The overall cycle time saving can be significant, while linear motors are also quiet and suffer minimal wear. Typical payload capacity is a few kilograms. Phaser MF linear-motor robots fitted with flux magnets can transport objects up to 160kg at high speeds.
Simulation and Setup
When evaluating single-axis robots for an application involving one or more units, the supporting tools to enable setup and troubleshooting should also be considered. Yamaha’s web-based simulator helps select the optimum specification. Users can quickly calculate important criteria like the projected cycle time and ball screw lifetime after describing a few basic parameters.
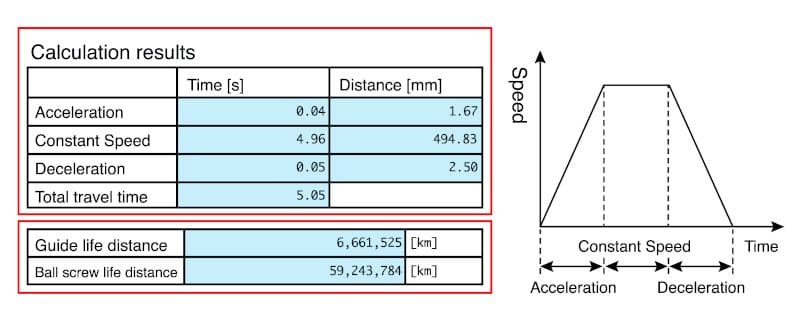
When setting up the system, the EP-01 robot controller works with the EP Manager PC application to assist with analysis and fine-tuning. Users can enter extensive details of the usage conditions, including transport mass, point data, and operation type. This makes it possible to assess the performance in a virtual environment without running real hardware. simulation provides comprehensive results including the total operating time, time for individual operations, maximum speed, and acceleration.
When setting up and running the robot system on the factory floor, EP Manager gives important information like real-time tracing of actual speed, motor load status, and the time to reach specific positions. Continuous monitoring is possible to verify the setup and enable long-term analysis and troubleshooting assistance.
The tool also provides real-time tracing and allows checking of the alarm history, which supports maintainability. The alarm history check helps analyse errors by giving insight into parameters including position, speed, operating conditions, current value, voltage, and I/O status. Analysing these various states can help identify the root cause of the alarm. In addition, real-time tracing allows users to analyse status up to the point an error occurred, to help identify causes such as overloading of the motor.
The EP-01 controller generates a feedback pulse output on a dedicated channel separate from the standard network connection. This helps with analysis and monitoring by providing continuous up-to-date position information that is independent of any communication delays on the network. By providing real-time output of the robot’s current position, the feedback pulse also enables speed ripple compensation.
Special Options
Special design features of the Robonity single-axis series include access to fixing points that allow each unit to be installed quickly and easily from either top or bottom without removing any exterior parts.
For applications that demand the shortest possible cycle time, Robonity AGXS models can accelerate/decelerate at up to 2g compared to conventional units that have a typical maximum of 0.5g. The AGXS (figure 4) is an advanced series that features ground ball screws for high accuracy and durability.
AGXS robots come ready for use in clean areas such as food preparation and production of cosmetics or pharmaceuticals. They feature stainless dust-proof covers and their low-friction rollers minimise grinding that generates dust and particles. A suction port is provided to safely remove any foreign matter from the mechanisms.
Conclusion
Single-axis robots provide an effective foundation to integrate robots in automated processes. Advantages include easy selection, design, and use. Key selection criteria include high rigidity, compact dimensions, and servo, stepper, or linear motor drive for optimum acceleration and speed. Effective tools for simulation and analysis can provide an important differentiating factor that significantly ease setup and long-term maintenance.